Prototyping
- Stephen Tlaker
- May 11, 2020
- 2 min read
Updated: May 15, 2020
The topic of my thesis is based on mobile virtual reality so I initially felt that I had not many options with regards to creating a physical 3D object but through my research during my literature review I found that the use of Bluetooth controllers are favourable in terms of navigation and interacting with the virtual world.
I experimented with blu tack to sculpt a low fidelity prototype before going to Sketchup and while this helped from a ergonomic point of view it was not suitable as the body temperature from my hand caused the shape to warp and stay consistent. When using SketchUp it was a challenge designing an object like this especially due to how 3D printed objects need to take things like gravity into consideration. That being said, I found a solution by dividing the parts seperatley and having them fit together after being printed.

As mentioned, I was looking at this from a ergonomic perspective so it was important to get the size right for the handle and buttons as well as the shape of the grip. I had intentions of curving the edges, a feature that I was familiar with in SolidWorks but this feature was not available unless I purchased a user made extension which was not viable. Regardless this would have involved having to divide the object into more parts as 3D printers are unable to print fully round objects as the resin was simply fall through. This Bluetooth controller prototype is made up of four parts; the handle, the trigger, a thumbpad for the joystick and the joystick itself. Each was made in a way that would be able to be printed (had I access to the printer in UL) and then later assembled. I was able to do this by starting with the handle and cutting out pieces to later be modified. If for whatever reason the pieces did not fit together then they could easily be gently sanded on one side to reduce the size by a fraction thus allowing them to fit.



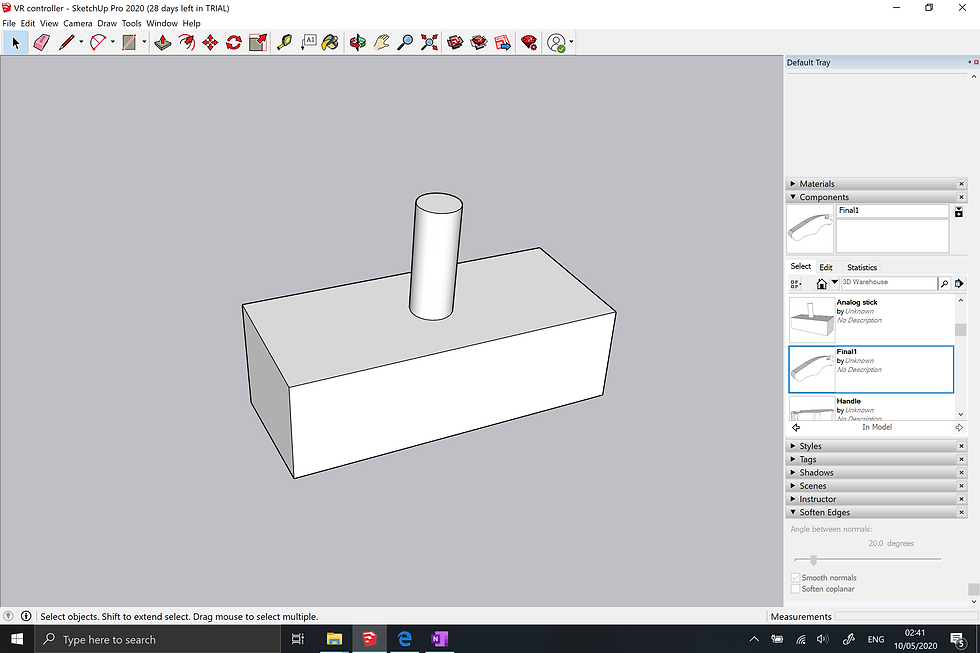
Comments